
Kärcher K 2 Nettoyeur haute pression (1400 W, 110 bars, 360 l/h), Noir/jaune, K 2 Premium Full Control 1400 wattsW : Amazon.fr: Jardin
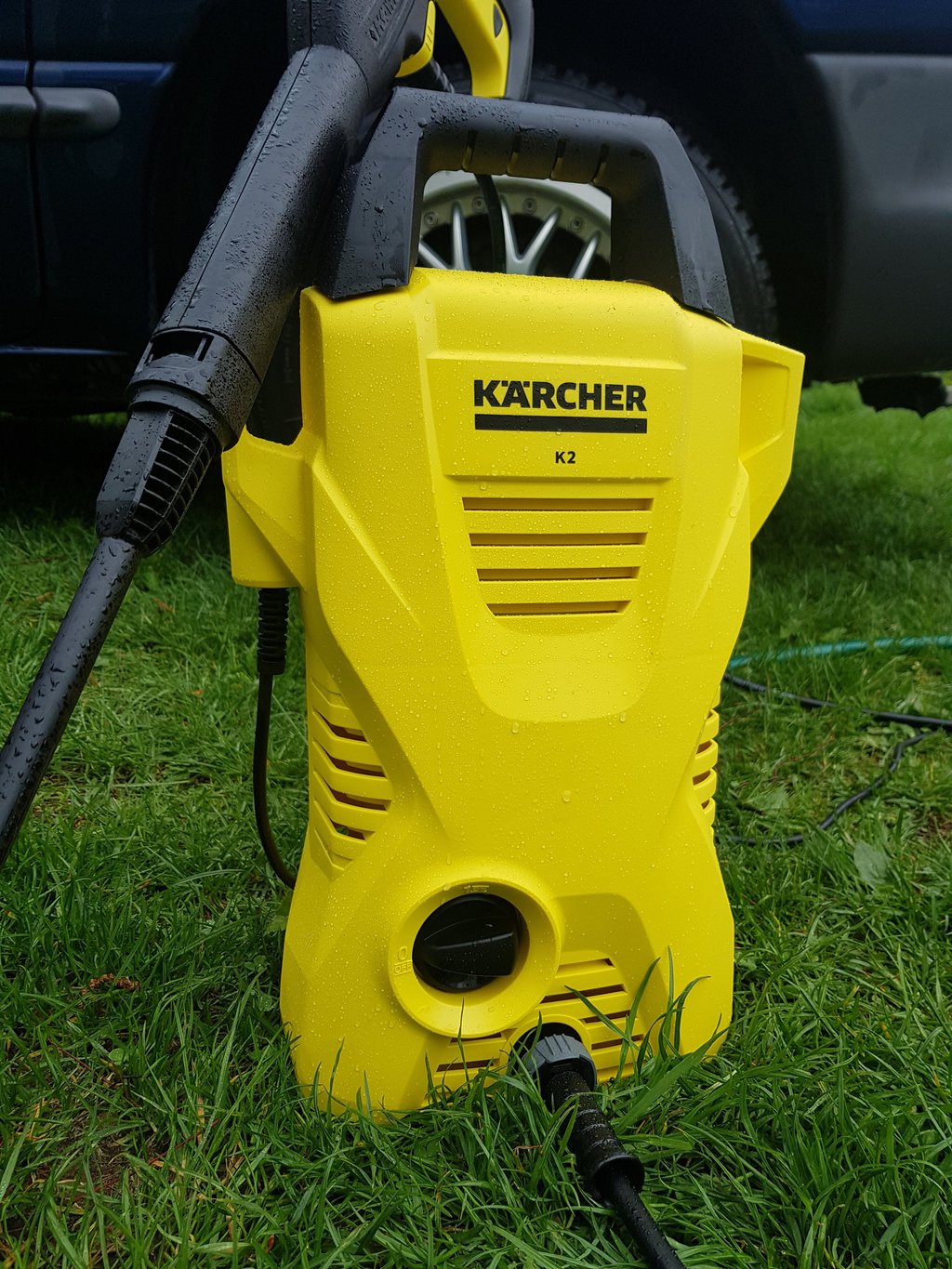
Karcher K2: mała, lekka, tania – ale czy przydatna? Szybki test budżetowej myjki ciśnieniowej. | agdManiaK
1.673405.0 myjka давление k2 full control 110 бар nr1 купить бу в Казани по цене 8010 руб. Z25532020 - iZAP24
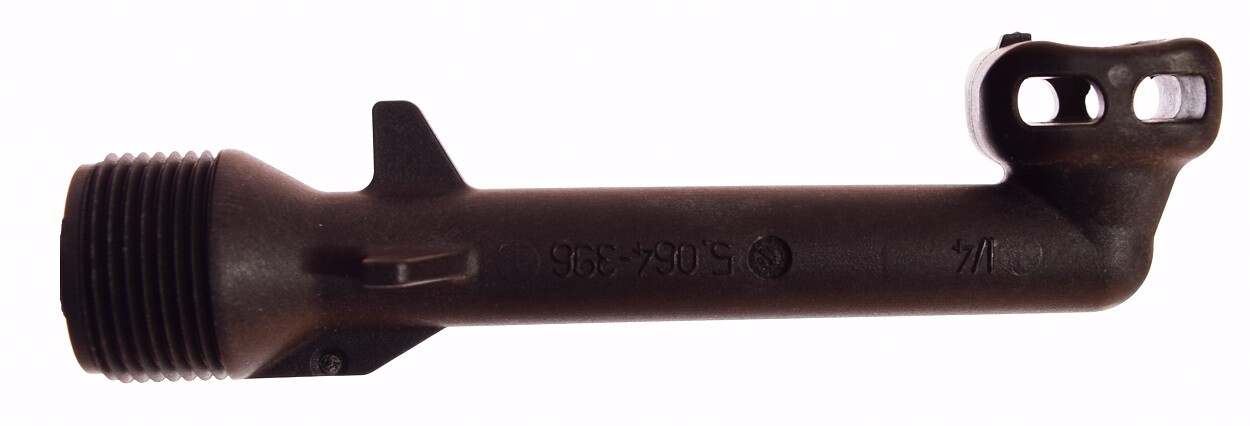